To provide an alternative solution for the disposal of food waste from the stores.
Our solution
When SUEZ first partnered with the supermarket, there was no reverse logistics operation in place at any of their stores in South West England.
Reverse logistics is the process of diverting goods from their typical final destination when there is an opportunity to capture any remaining value through another process before proper disposal.
SUEZ designed a solution for food waste recognising that a change from an individual store-side collection service to a backhaul system would achieve substantial cost savings, along with a significant decrease in environmental impact due to reduced vehicle movements.
In order to create the new process, SUEZ worked closely with the customer and the logistics partner – starting at the store and going right the way through to the disposal method via anaerobic digestion. During implementation changes to the store, processes were required. However, these were limited as much as possible to minimise the impact on the customer’s existing day-to-day operations.
Food waste collection system at retail park sites
The results
The customer benefitted from a reduction in costs of 48%, equating to approximately £170,000 annually.
The new system was implemented effectively via a communications campaign to ensure that all staff involved in the process understood how it worked and what was required of them. In addition to the cost-savings, the carbon footprint has also reduced as a result of fewer vehicle movements and use of reverse logistics capacity, which would otherwise have been wasted.
As a direct result of this new system for food waste, approximately 150 tonnes per year is diverted from general waste, generating cost savings of £10,000. This represents an improvement in environmental performance by capturing this material for anaerobic digestion.
The backhaul system was highly successful, having initially been designed and implemented for food waste across the South West it can now be used as replicable model. The customer can apply the same process to materials such as card and plastics in order to achieve even greater savings in transport cost, environmental footprint and overall efficiencies in its recycling regime.
food waste diverted from general waste each year
(approximately)
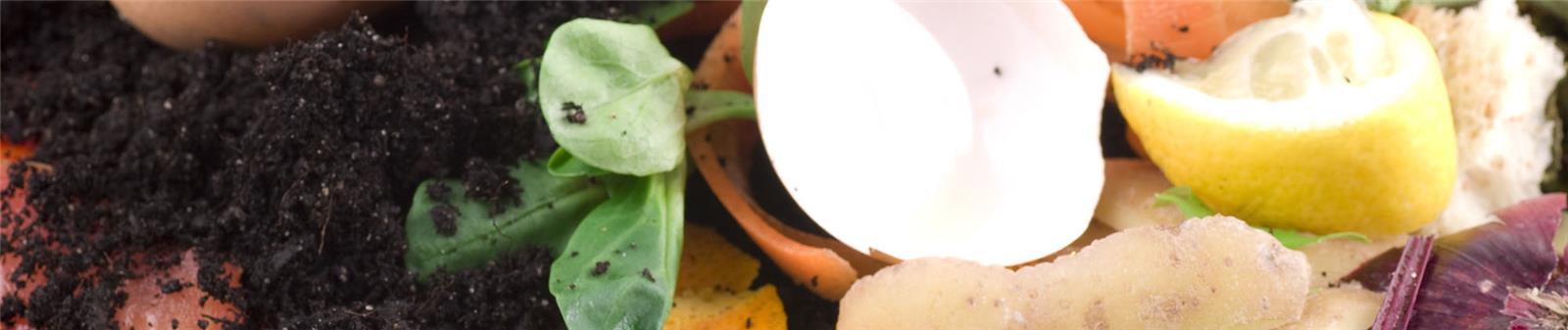